De snelheid van logistiek is tegenwoordig zo enorm dat bijna elke seconde telt. Maar als die seconden zo enorm tellen, hoe kan het dan dat we zo weinig aandacht besteden aan onze werkplek en de organisatie daarvan? In lean termen duiden we die werkplekorganisatie ook wel aan met 5S. Een ogenschijnlijk simpel concept, maar wat oh zo moeilijk blijkt te zijn in de praktijk. Hoe komt dat? En wellicht belangrijker: wat kun je daaraan doen?
Wie weet herken je dit: je komt op je werkplek en het gereedschap of heftruck is onvindbaar. En heb je het gevonden, dan blijkt bijvoorbeeld de accu leeg. Dit soort kleine ergernissen zijn een briljant signaal om daar iets aan te doen. Want bedenk maar eens hoeveel tijd dit soort – simpel te voorkomen – gedoe ons kost? En wat blijkt, wanneer we dit gedoe weten op te lossen creëren we gelijk een prettigere werkomgeving en zelfs werkgeluk. Handig in een krappe arbeidsmarkt!
De vijf S'en van 5S
Eerst even een korte uitleg waarom die werkplekorganisatie ook wel 5S wordt genoemd. Dat staat voor een vijftal stappen die elk beginnen met een S (zowel in het Japans, Engels als Nederlands). In het Nederlands staan ze voor: scheiden, schikken, schoonmaken, standaardiseren en standhouden. Die laatste kennen ze bij Japan in Toyota niet, omdat standhouden in hun DNA zit. En daar zit net de kneep hier in Nederland. We hebben moeite iets vol te houden.
Sterker nog, we komen vaak niet verder dan de derde S, schoonmaken. En zelfs die is meer dan schoonmaken, het gaat vooral om inspecteren tijdens die schoonmaak. Denk maar eens aan een vervuilde werkplek, waar tijdens het schoonmaken wordt geconstateerd dat een machine olie lekt. Terwijl men dacht dat die olie er eigenlijk altijd al lag. Men ziet die vervuiling als normaal. Dat is gelijk een bruggetje naar ‘het nieuwe normaal’, ofwel de nieuwe standaard.
Standaard als basis
Hier zit tevens een deel van de essentie van een lean aanpak, een helder beeld van hoe iets gedaan moet worden, eruit moet zien of hoe iemand getraind moet zijn. Dat noemen we een standaard, wat bij menigeen een beeld oproept van een vastgeroeste afspraak. Niets is minder waar. Een standaard kun je zien als een ‘beste manier van werken’, zoals we die nu kennen. Maar die ‘beste manier’ is aan verandering onderhevig. Wat gisteren goed leek, kan vandaag beter en volgende week nog beter.
De crux is betrokkenen dat zelf aan te laten passen (na afstemming met overige betrokkenen), dat zorgt voor het nodige eigenaarschap. Want als we anderen de standaard laten beschrijven, werken we het probleem van ‘scheiden van denken en doen’ in de hand. Terwijl we vanuit de lean gedachte van ‘respect’ ieders kennis optimaal willen benutten. Ook kun je het principe van ‘er alles aan doen om elkaar te begrijpen’ gebruiken. Hierdoor zal de beschrijving al snel een visuele insteek krijgen, denk maar aan hoe kinderen Lego-pakketjes in elkaar kunnen zetten. Een afwijking valt dan vrij snel op.
Afwijkingen worden zichtbaar
Dit brengt me op de reden van 5S, dat we eenvoudig afwijkingen kunnen zien. Ziet een werkplek er altijd verzorgd uit, en opeens niet meer? Dan kun je je, als manager of collega, afvragen of er iets aan de hand is. Heeft iemand het te druk? Zijn er andere problemen? Dit alles met de insteek te zorgen dat die persoon hulp kan krijgen, in wat voor vorm dan ook. Wat we zijn allemaal mens, die graag trots is op zijn of haar werk.
Als management moet je zoiets faciliteren. “Wat heb jij nodig om je werk goed te doen?” is een mooie hulpvraag. Dan is mijn vraag aan jou: “Wat ga jij vandaag doen, om het morgen beter voor elkaar te hebben?” Kom je er niet uit? Neem dan gerust contact met mij op, ik help je graag verder.
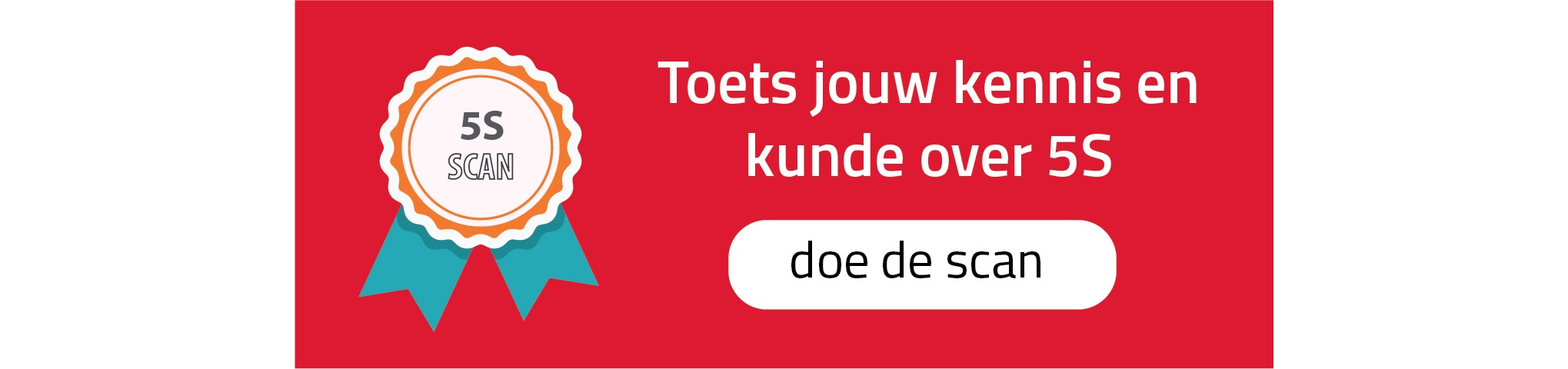
Toyota Material Handling organiseert regelmatig hands-on workshops waarin u de kracht van 5S ervaart en ook concrete handvatten krijgt om de vijf stappen in de praktijk toe te toepassen. Deze workshops vinden plaats in Ede.